is everyone’s job
Prioritizing the Planet
At Hunter, we feel it’s our responsibility to be a steward of the environment. That’s why we put a great deal of effort into minimizing our impact on the planet while safeguarding it for future generations. To support this endeavor, we continually seek ways to become more sustainable. This involves monitoring and assessing our business activities, then enacting plans to minimize our impacts and, when possible, eliminate them entirely.
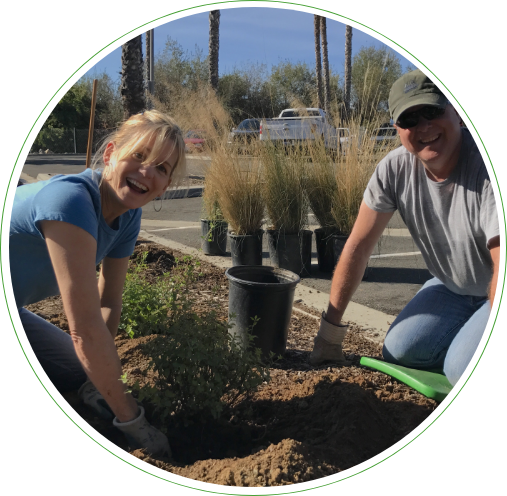


Goal
50%
Achieve a 50% reduction in Scope 1 and Scope 2 emissions from our 2019 baseline by 2030; measure Scope 3 emissions by 2025.
How We're Doing2022
We saw an increase in emissions to 20,195 metric tons of CO2e from our 2019 baseline of 19,464 metric tons of CO2e.
Climate Impacts and GHG Emissions
Taking steps to better understand our climate impacts and greenhouse gas emissions is a top priority for us. We’ve continued to implement the Climate Action Plan we developed in 2021, including making significant investments in energy efficiency projects and renewables. Despite these ongoing efforts, our emissions rose slightly from 2021 and our 2019 baseline.
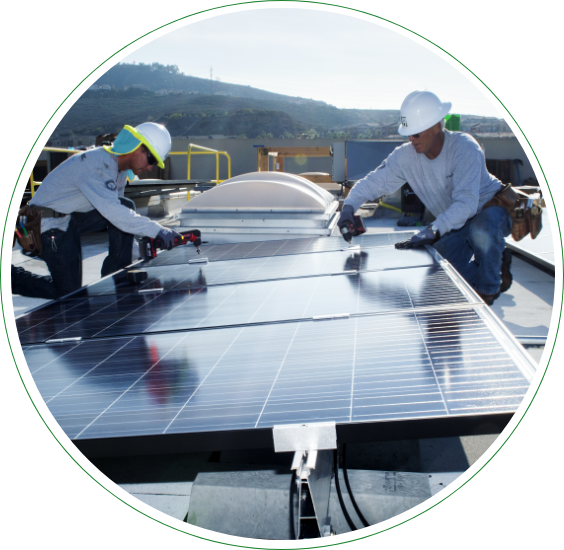
Energy Use and Renewable Energy
Across our company, over 80% of our greenhouse gas emissions come from the energy we purchase from local utilities. We’re committed to reducing the energy used during our manufacturing processes and growing our on-campus renewable energy generation capabilities. By proceeding with the Climate Action Roadmap we created in 2021, we’ve been able to continuously work toward increasing our renewable energy generation on-site at our manufacturing facilities.

Goal
2022
Complete a Life Cycle Assessment (LCA) in 2022 for one of our best-selling product lines.
How We're DoingWe vetted vendors and contracted with one in 2022. Although the process is taking longer than expected, it should be completed by the end of 2023.
Product Responsibility
We incorporate quality and sustainability into everything we make, designing each product with high-end materials and cutting-edge features that deliver long-lasting performance while minimizing our environmental footprint. Though supply chain issues continued throughout 2022, we took calculated steps to ensure we had access to the raw materials needed to manufacture our products.
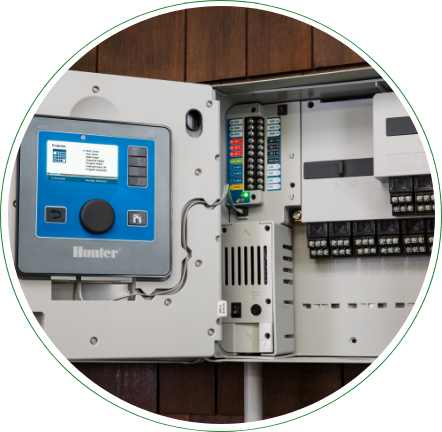
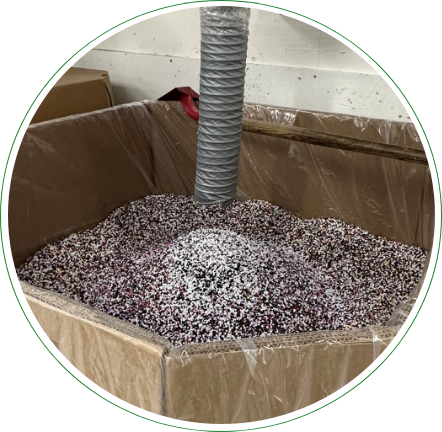
Waste
As a manufacturing company that produces scrap waste and delivers products in packaging, we know that waste will always be a material topic for us. We’ve developed a two-pronged approach to this issue: reducing the waste we produce and finding creative and responsible ways to process the waste we can’t prevent.
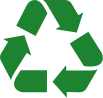
Goal
90%
Achieve zero net waste by diverting at least 90% of our waste from landfills by 2030.
How We're Doing79.7%
We recycled and diverted 79.7% of our waste from landfills across our three main manufacturing campuses.
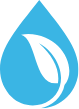
Goal
30%
Reduce water consumption by 30% against our 2019 benchmark by 2030.
How We're Doing27%
We've reduced our water consumption by 27% to date compared to our 2019 benchmark.
Water Use
As a leading manufacturer of irrigation solutions, water is a key material issue for our organization. Our stakeholders feel strongly that this is an important aspect to address as it relates to our environmental impact. Today, our goal focuses on the water footprint we control directly at our facilities. Our San Marcos, California, and Tijuana, Mexico, facilities are located in climates that experience extreme drought. We acknowledge that this reality makes our water conservation efforts even more critical.